機械(xiè)加(jiā)工中影響(xiǎng)毛刺變化的主要因素
時間:2018-05-21 16:33:25作者:LeeZhou來源:德高潔清潔設(shè)備
機械零件在加工製造過程(chéng)中,即便是精加工過程(chéng)也不(bú)可避免(miǎn)的會有毛刺(cì)。毛刺的種(zhǒng)類繁多,對零件的加工精度、裝配精度、再加(jiā)工定位和外觀質量等許多方麵都會產生不良影響。
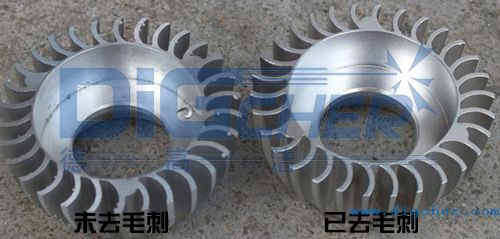
機械加工中(zhōng)容易產生毛(máo)刺的幾個(gè)部位:
1、鑽/鏜孔時,孔(kǒng)的進口及出口處會產生毛刺和翻邊,特別是出口處的毛(máo)刺會(huì)比較多。
2、銑麵時,在被加工工件表麵的邊、角、棱處會產生較多的毛刺。
3、鑽各交叉孔,尤其是傾斜交叉孔時,更容(róng)易產生較大、較多的毛刺。
毛刺的形成依賴於工(gōng)件與刀具在切削過程中的相對運動。影響毛刺生成及變化的主要因素(sù)有工件材料、切削(xuē)用量、刀具參數和加工方法等。各因素之間互相(xiàng)影響、互相製約。工件經過切削加工(gōng)之後,其邊、角、棱等(děng)部位上是(shì)否產生毛刺(cì),毛刺的尺寸大小及形狀如何變化等將取(qǔ)決於諸多影響因素的綜合作用。
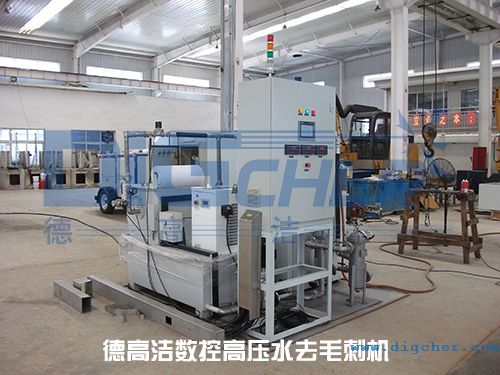
1、合理安排加工順序
盡量將產(chǎn)生毛刺的(de)工序(xù)安排在前,而把不產生毛(máo)刺(或毛刺較小、數量(liàng)較少)的工序安排(pái)在後。
2、合理的加工方法
工藝設計時應選擇合理的加(jiā)工(gōng)方法,盡量減少後(hòu)道工序去毛刺的成本。在不影響生產效率和加工成本的前提(tí)下,盡可能選用(yòng)生成毛刺(cì)較少的(de)加(jiā)工方法。
3、合理選擇切削方向
零件棱角越大(dà),切削層(céng)末端根部剛(gāng)性越(yuè)大,切削層材料越易於被完(wán)全切離,毛刺產生的數量和大小會越小。選擇合理的切削走刀方向,使最後的出刀口位(wèi)於零件棱角較大的部位。
4、采用多件疊合的加工方法
這種方法適合於外形(xíng)尺寸相同、加工麵能緊密結合的零件。
5、采用少無毛刺的加工工藝
對於要求嚴格控製毛刺(cì)的某些精密零件加(jiā)工時,可采用少無毛刺的先(xiān)進加工工藝。
6、選擇(zé)合(hé)適的去毛(máo)刺工藝
合理選用恰當(dāng)去毛刺工藝對提高生產效率和產品的質量、降(jiàng)低製造成本起著重要的影響(xiǎng)。人工去(qù)毛刺適用於毛刺小結(jié)構(gòu)簡單的產品;研磨去毛(máo)刺適(shì)合批量較大的小產品;高壓水射流技術適用(yòng)於精密零件去毛刺;超聲(shēng)波去(qù)毛刺主要針對(duì)微觀毛刺。
北京德高潔清潔設備有(yǒu)限公司根據多年高壓(yā)水射流技(jì)術經驗,研發出數控加工中(zhōng)心去毛刺機、回轉式高壓水去毛(máo)刺機和數控去毛刺加工清洗線,可適用於(yú)多種不同零件的去毛刺任務(wù),同時完成去毛(máo)刺、精(jīng)清洗、烘幹相結合。
要真正清除機械加工過程中的毛刺,還要注(zhù)重提高管理者和(hé)操作者的質量意識,不忽視每一個環節,把好質量關,才能更好的解決問題(tí)。
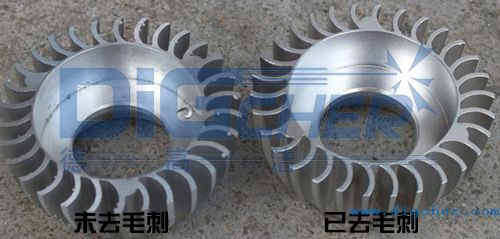
機械加工中(zhōng)容易產生毛(máo)刺的幾個(gè)部位:
1、鑽/鏜孔時,孔(kǒng)的進口及出口處會產生毛刺和翻邊,特別是出口處的毛(máo)刺會(huì)比較多。
2、銑麵時,在被加工工件表麵的邊、角、棱處會產生較多的毛刺。
3、鑽各交叉孔,尤其是傾斜交叉孔時,更容(róng)易產生較大、較多的毛刺。
毛刺的形成依賴於工(gōng)件與刀具在切削過程中的相對運動。影響毛刺生成及變化的主要因素(sù)有工件材料、切削(xuē)用量、刀具參數和加工方法等。各因素之間互相(xiàng)影響、互相製約。工件經過切削加工(gōng)之後,其邊、角、棱等(děng)部位上是(shì)否產生毛刺(cì),毛刺的尺寸大小及形狀如何變化等將取(qǔ)決於諸多影響因素的綜合作用。
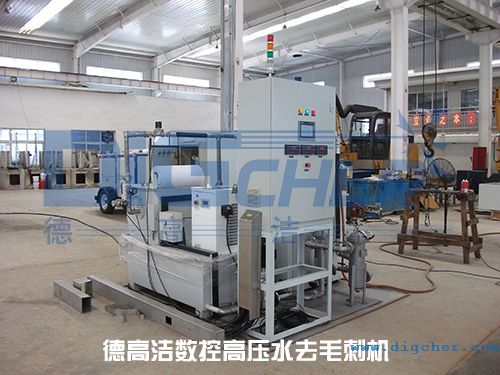
1、合理安排加工順序
盡量將產(chǎn)生毛刺的(de)工序(xù)安排在前,而把不產生毛(máo)刺(或毛刺較小、數量(liàng)較少)的工序安排(pái)在後。
2、合理的加工方法
工藝設計時應選擇合理的加(jiā)工(gōng)方法,盡量減少後(hòu)道工序去毛刺的成本。在不影響生產效率和加工成本的前提(tí)下,盡可能選用(yòng)生成毛刺(cì)較少的(de)加(jiā)工方法。
3、合理選擇切削方向
零件棱角越大(dà),切削層(céng)末端根部剛(gāng)性越(yuè)大,切削層材料越易於被完(wán)全切離,毛刺產生的數量和大小會越小。選擇合理的切削走刀方向,使最後的出刀口位(wèi)於零件棱角較大的部位。
4、采用多件疊合的加工方法
這種方法適合於外形(xíng)尺寸相同、加工麵能緊密結合的零件。
5、采用少無毛刺的加工工藝
對於要求嚴格控製毛刺(cì)的某些精密零件加(jiā)工時,可采用少無毛刺的先(xiān)進加工工藝。
6、選擇(zé)合(hé)適的去毛(máo)刺工藝
合理選用恰當(dāng)去毛刺工藝對提高生產效率和產品的質量、降(jiàng)低製造成本起著重要的影響(xiǎng)。人工去(qù)毛刺適用於毛刺小結(jié)構(gòu)簡單的產品;研磨去毛(máo)刺適(shì)合批量較大的小產品;高壓水射流技術適用(yòng)於精密零件去毛刺;超聲(shēng)波去(qù)毛刺主要針對(duì)微觀毛刺。
北京德高潔清潔設備有(yǒu)限公司根據多年高壓(yā)水射流技(jì)術經驗,研發出數控加工中(zhōng)心去毛刺機、回轉式高壓水去毛(máo)刺機和數控去毛刺加工清洗線,可適用於(yú)多種不同零件的去毛刺任務(wù),同時完成去毛(máo)刺、精(jīng)清洗、烘幹相結合。
要真正清除機械加工過程中的毛刺,還要注(zhù)重提高管理者和(hé)操作者的質量意識,不忽視每一個環節,把好質量關,才能更好的解決問題(tí)。
上(shàng)一篇:【雙效合一】數控高壓水去毛刺加工清洗線
下一篇:發(fā)動機(jī)鋁合金(jīn)汽(qì)缸蓋加工去毛刺方法
熱門搜索: